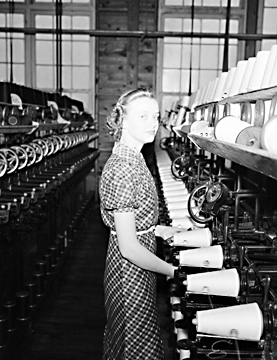
The task system was part of an industrial management trend that relied on so-called scientific theories to scrutinize and enhance worker task performance. On the national scene, Frederick W. Taylor, the "father of scientific management," with followers like Henry L. Gantt and Lillian E. Gilbreth, developed a system of manufacturing management that provided coordination and efficiency control of machines, materials, and workers. Gantt, for instance, devised a task-and-bonus system of compensation, a forerunner of later incentive plans. Under this system, workers received a guaranteed wage, but if they accomplished a measurable amount of extra work, they were paid a bonus (a percentage of the base rate). Taylor's doctrine included theories such as time and motion study, production planning, and inventory control. He also claimed that it was possible to determine "scientifically" how a particular human task might be done most efficiently. Labor unions and other pro-labor forces condemned the Taylor system because it diminished or in some cases removed the human qualities involved in job performance.